Textile laundry Newasco de Hoop is a family business that doesn’t shy away from technology. Through the usage of RFID tags, information is linked to all clothing coming through. Looking to further innovate their processes, they reached out to the MKBdoet program, a collaboration resulting in enormous time savings.
The current RFID tags are found in each item of clothing coming in. Handy for large clothing registrations. But with a daily supply of laundry-filled containers, individual scanning by hand remains a time-consuming operation.
So what if we could scan the laundry in bulk? The MKBdoet robotics innovation program and RoboHouse provide a unique discourse between engineer and entrepreneur. “All assumptions are analysed so we can then focus on the problem,” says Mark Bruijnen, program manager at RoboHouse. “This way we can truly help the entrepreneurs one step forward.”
“We look at it as engineers, and usually that is from a slightly different perspective than the entrepreneur.” Mark Bruijnen, project manager at RoboHouse.
So what if we could scan the laundry in bulk? The MKBdoet robotics innovation program and RoboHouse provide a unique discourse between engineer and entrepreneur. “All assumptions are analysed so we can then focus on the problem,” says Mark Bruijnen, program manager at RoboHouse. “This way we can truly help the entrepreneurs one step forward.”
A site visit proved the main difficulty lay in the positioning of the RFID tag in relation to the scanner. On top of that, the current setup meant that also the surrounding laundry would be scanned, influencing the margin of error.
“We set up a brainstorming session with Newasco where we put forward all ideas. The entrepreneur‘s practical experience and our technical experience complement each other, which leads to an idea that we further work out through rapid prototyping.”
“RoboHouse’s involvement, clear communication, and hands-on mentality suited the project, leading to a great collaboration.”Niels van Bremen, project lead at Newasco.
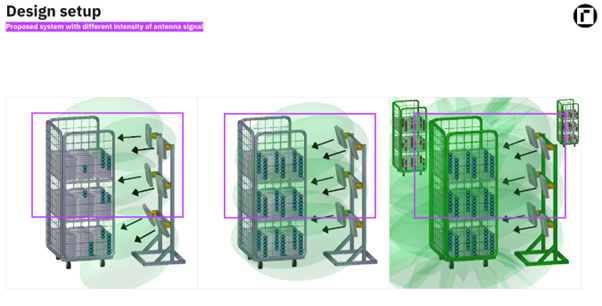
“Rapid prototyping means that a physical prototype is developed as quickly as possible. This allows for in-practice testing of all assumptions. A test setup mimics the real-world application and identifies chances and limitations, which is food for design iterations.”
The 12-week journey finally came to an end with a demo of the successful prototype. The prototype meant Newasco had a clear overview of all components needed, as well as a clear cost estimation. Newasco can now go on and look for a supplier with the help of RoboHouse’s advisory follow-up steps.
Does your company have a challenge in which technology and robotics could help? Contact Mark Bruijnen via email m.c.bruijnen@tudelft.nl or telephone 06-11008323.
Co-financed as part of the European Union’s response to the COVID-19 pandemic.