In our new RoboHouse Succes Series we highlight our latest successes, some of which take unexpected turns. Voestalpine is a German steel and technology group that “coats products to make them better”. In February last year we first met with Voestalpine to discuss options for full automation. Guus Paris, lead of the project at RoboHouse, tells us more about the achieved succes.
“Voestalpine approached us with the question if we could help them implement 3D camera’s in the factory, allowing a robot to unpack drill bits yet to be coated, sort them, put the bits in the oven, resort, and repack. Basically, automating the full process.”
However, after several conversations it turned out there was much more to it than just generic tasks. What at first sight seemed like the perfect opportinity to implement robotics, proved to be way more intricate, requiring worker’s expertise and precise judgement.
“One order often contains up to 50 different bits, leading to a real need of experience for proper placement.”Guus Paris, RoboHouse
“The drill bits are placed in a tray, cleaned and then transferred onto stacks. Finally, the right coating is applied to each bit in the oven. Although seemingly straight forward, the exact way these bits are placed in the tray is crucial for the process to yield positive results. The factory employees rely on their expertise to find the best configuration and can do this much faster than a robot can.”
“It was an unexpected turn of events,” Guus enthusiastically tells us. “Instead of a robot for the full process, we started asking ourselves: ‘what if we automate the tedious part of the job by digitalising all administrative factors?’. This way the workers can stick with the enjoyable part of the work and can leave a big portion of the paperwork behind.”
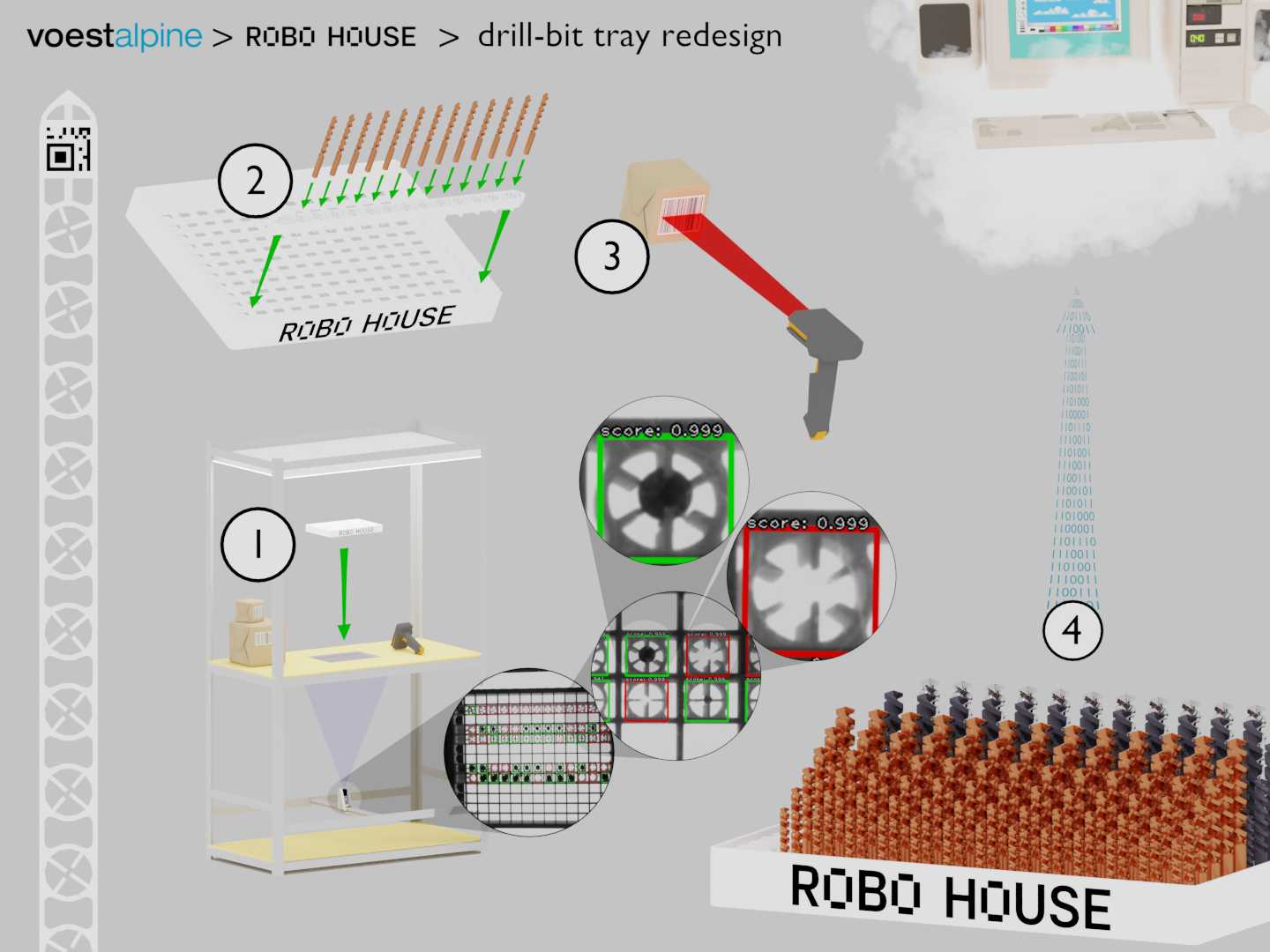
The solution RoboHouse and Voestalpine agreed upon was improving digital traceability. A system detects the bits and labels them with a QR code. The employee then uses his experience and puts the bits together in whatever way he sees fit, before putting them in the oven. This digitalisation of paperwork meant the millions of bits could be traced anywhere throughout the factory, something previously impossible.
“People often ask for a robot, but when you start thinking together you end up with something completely different.”Guus Paris, RoboHouse
So what is the real succes in this story? “In the Voestalpine case, the success was in the recognition that sometimes the employee’s work is way more complex than thought beforehand. The openness of Voestalpine and the length of the project lead to a succesful conclusion that implementing robotics not to automate the entire process, but just the less enjoyable parts of the work: something all parties celebrate.”
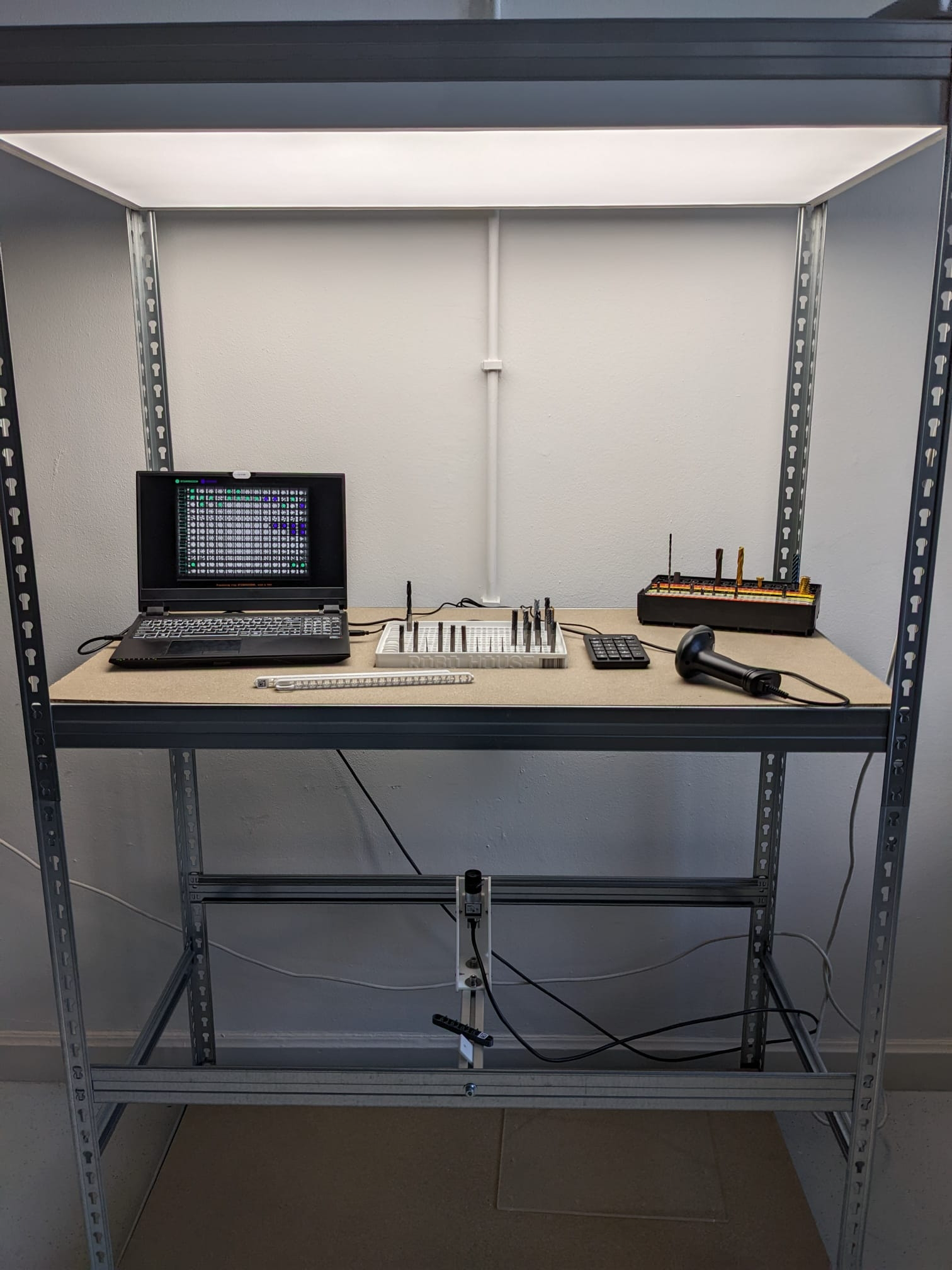