Students of Delft University of Technology have developed a new add-on for a 3D printer that can cast silicones inside a 3D printed shell during the printing process. This new, and cheap, technique can be used to create new soft-robotic products that were previously impossible to make. The team presented their findings yesterday, at the science fair that marked the end of the minor Advanced Prototyping of the faculty Industrial Design Engineering.
The technique they developed is called UltiCast. “It is a combination of moulding and 3D printing”, explains Max Nobel, student Industrial Design Engineering. “The machine makes a plastic shell, which is filled with 2-components silicones at the same time.” The shell is made of a plastic (PVA) which dissolves in water. The team uses a Ultimaker 3D printer, which they completely rebuilt.
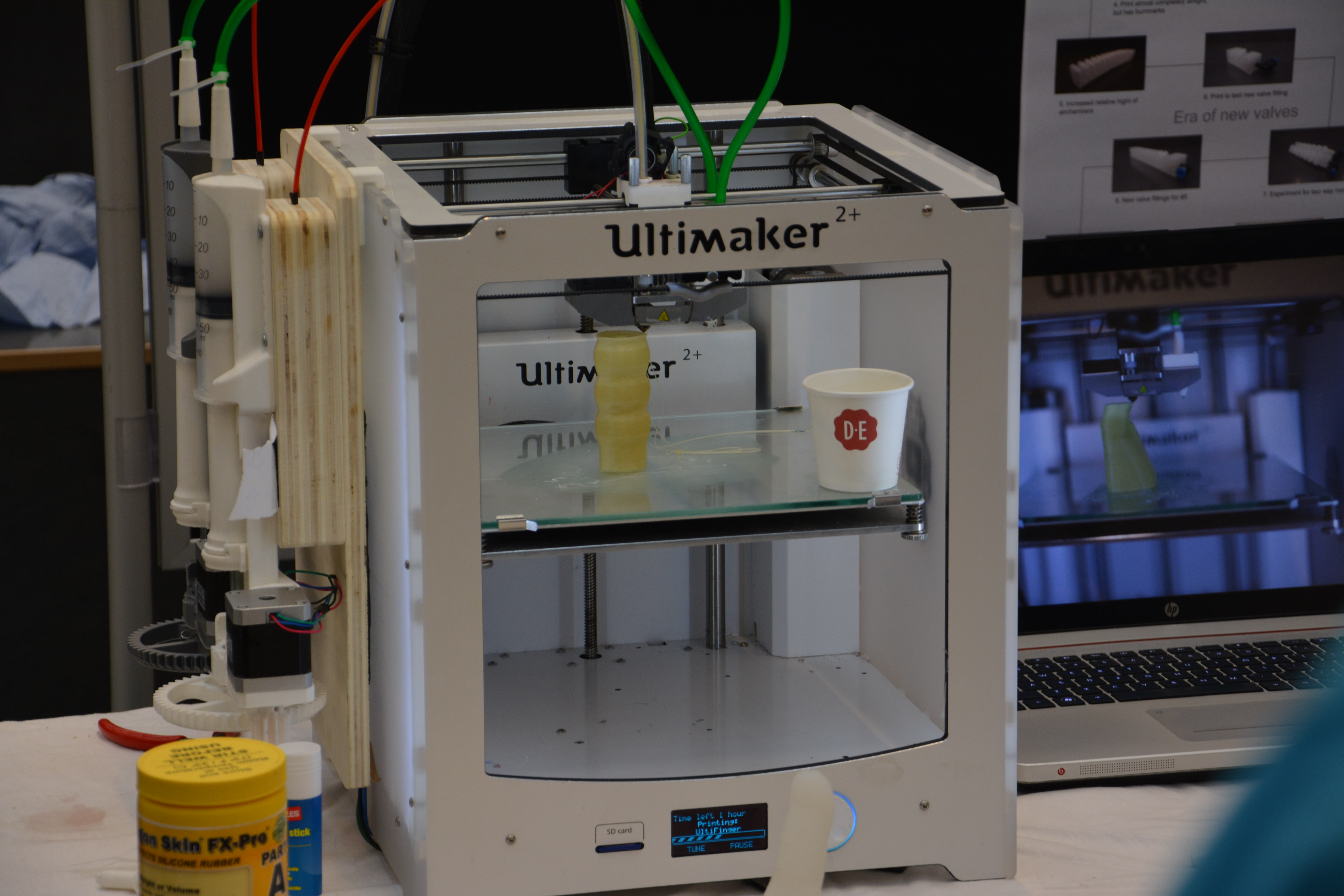
UltiCasting will allow more complex shapes that could not be printed on a ‘traditional’ direct drive 3D printer. If the mould quality is high, the surface quality of the flexible silicon will also be very high. This is very hard to achieve in traditional fused deposition modelling (FDM) printing, because every layer of hot filament deforms the previous layers of filament.
Soft robotics
The new technique proves very interesting for soft robotics. With UltiCasting it becomes possible to ‘print’ a soft actuator in a mould, thereby elimination the manual casting process and doing so speeding up the process of creating soft actuators. “You get a lot of freedom to personalise the behaviour of robots with geometry and materials”, tells team member Rob Scharff, a PhD student in soft robotics.
It is mechanical intelligence. “You make sure that the robot behaves exactly as you want to.” For example, you can make a robot hand with flexible fingers and a thumb that has enough strength to pick up a vegetable. “With 3D printing, you can fabricate a custom-made gripper.” Besides, it has the potential to mix hard materials – as another team proved – making it possible to print a skeleton inside silicone. “You can use various materials during printing. The results are much more complex materials.”
The new application is cheap as well: the setup the students made cost about €3000, says Scharff. Other complex multi-material 3D printing systems cost around €300,000. “That’s a big difference.”
Medical sector
In the field of soft robotics, cheap 3D printing can prove valuable for several applications. This could be the case in the medical sector, especially with aided movement. “Reducing the cost of treatment and support utilities is a goal that inspires us all. Soft robotics could, in the long term, be a big player in this progress”, the team states.
Therefore, they developed a 3D printed glove with soft robotics actuators to help move your fingers. This glove could be used to assist people with arthritis, local paralysis, limited hand function or as supporting tool in rehabilitation. The goal of the team is not to create a finished product, however, but rather to give a proof of concept showing the possibilities of 3D printing for soft robotics.
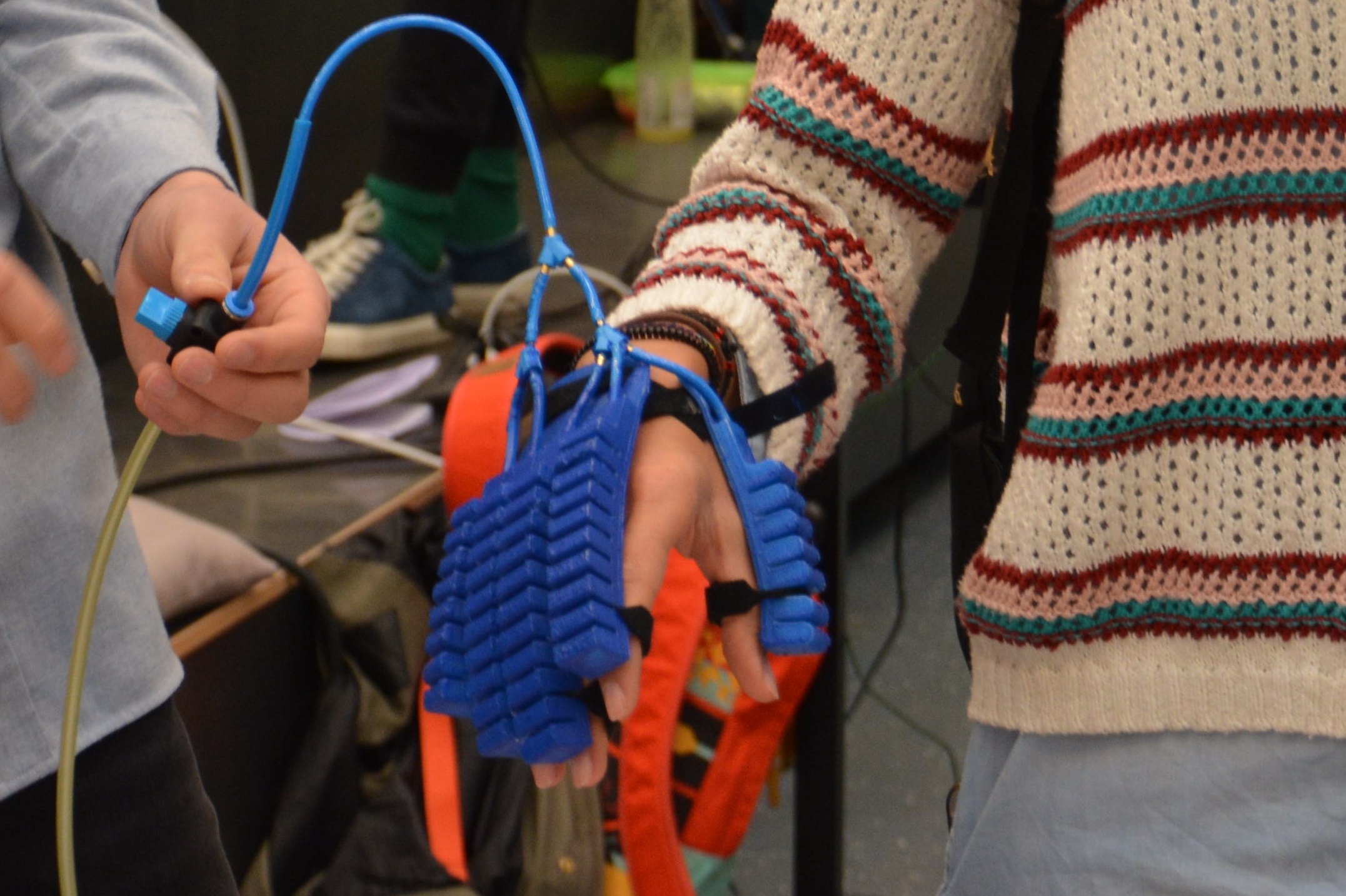
Digital fabrication
“3D printing offers a variety of applications, being soft robotics one of them”, tells coordinator Jouke Verlinden. “It allows you to make things that are impossible with traditional robotics. Soft robotics is a research theme in which we invest a lot.”
At the science fair, other student- projects were on display as well. At first sight, some of them don’t seem to be related with robotics. Others are. But don’t be mistaken! “It is all part of digital fabrication. Project Michelangelo is clearly a robot, but the Hololens at the museum has a lot to do with robotics as well. It is all about image recognition, and in the basis, they work with the same algorithms as the ones that are being used for robotic visioning.”