The students follow an exciting programme that brings them into contact with all aspects of developing real robots. The students work in a multidisciplinary team to develop their own robot according to their own market and application research. During the programme, the student teams are based in RoboHouse.
Demo Day
On 30 January 2019, the results of the minor robotics were shown during the Demo Day in the Science Centre.
Delta, the journalistic platform of the TU Delft reported on the Demo Day (article in Dutch).
Following we present the projects that the students of the 2018-2019 minor developed.
Team 1 Easy Cheesy
Cheese Ripening Robot
The innovative robotics company Lely, know for its autonomous milking robot, is continuously exploring new markets and products. Like last year, they are participating in the Robotics Minor of the TU Delft, and this year a team has been working on a fully autonomous cheese ripening robot. The robot can drive through a cheese ripe- ning warehouse and handles the entire ripening process of over 3500 cheeses of about 16 kg. This means it has to regularly turn the cheeses, to prevent them from bulging out due to gravity. Furthermore, the cheeses have to be coated with a moulding agent to prevent the cheese from spoiling.
This project is commissioned by Lely.
Team 2 LOBSTER
LOBSTER
The deep sea is one of the most fascinating environments on Earth. However, most of the deep sea remains uncharted territory due to its extreme conditions. To explore the deep sea, a large and expensive robot is needed which has to be deployed and operated from an even more expensive ship.
This has two reasons. The first reason is that the robot needs to be controlled remotely because the robot has to be able to do precise movements with its arms. However, seawater blocks most types of communication which means they use a tether from the robot to the ship which has to be held into place. Keeping the ship in place uses a lot of fuel and the crew and operators aren’t cheap either. The other reason is that the robots’ tether is heavy and thus requires the robot to have strong thrusters to move itself, making the robot bigger.
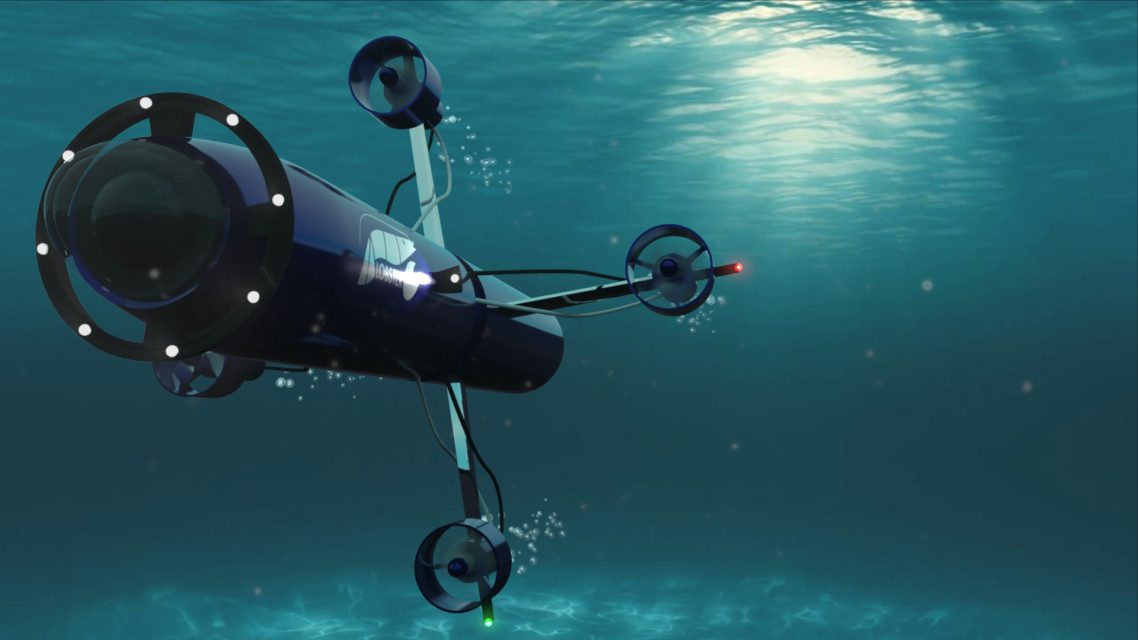
The plus point is that these robots can do everything. They have arms that can be used to manipulate objects, take samples, catch fish or even repair structures. However, sometimes you just want to take a look. In that case such a robot is overkill.
This is where LOBSTER comes in. We aim to make deep sea inspection, prospecting, and research accessible by developing a small, fast, low cost and autonomous deep sea robot that can reach the seabed quickly, take pictures, make measurements and return to the surface. We are using our first advanced prototype for testing. Our goal is to have a robot that is able to reach a depth of 2 kilometres by the end of January 2019.
Team 3 Bolts ‘n Bears
Weed Whacker
We have been working on making an ecological solution for one of today’s biggest agriculture problems; removing unwanted weeds between crops without the use of harmful herbicides. We will be working closely with our client: Odd.Bot, a young start-up, with the aspiration to build autonomous systems that create value to society. The prototype and documentation our team will provide, should be a stepping stone to this future.
Currently farmers use heavy, human controlled tractors with trailers which can only remove the weeds in between rows of crops. The other weeds are removed using herbicides, which also end up in the environment and the harvested crops and so eventually our food. Another growing problem with the use of herbicides is the developing resistance of the weed to herbicides, so it is certainly not a long-term solution. Another disadvantage of the current process is the reduction of the soil fertility by condensing the upper layer of ground underneath their enormous wheels and weight of the tractors. These machines also require a fair amount of fossil fuels, so it contributes on climate change with its CO2 emissions.
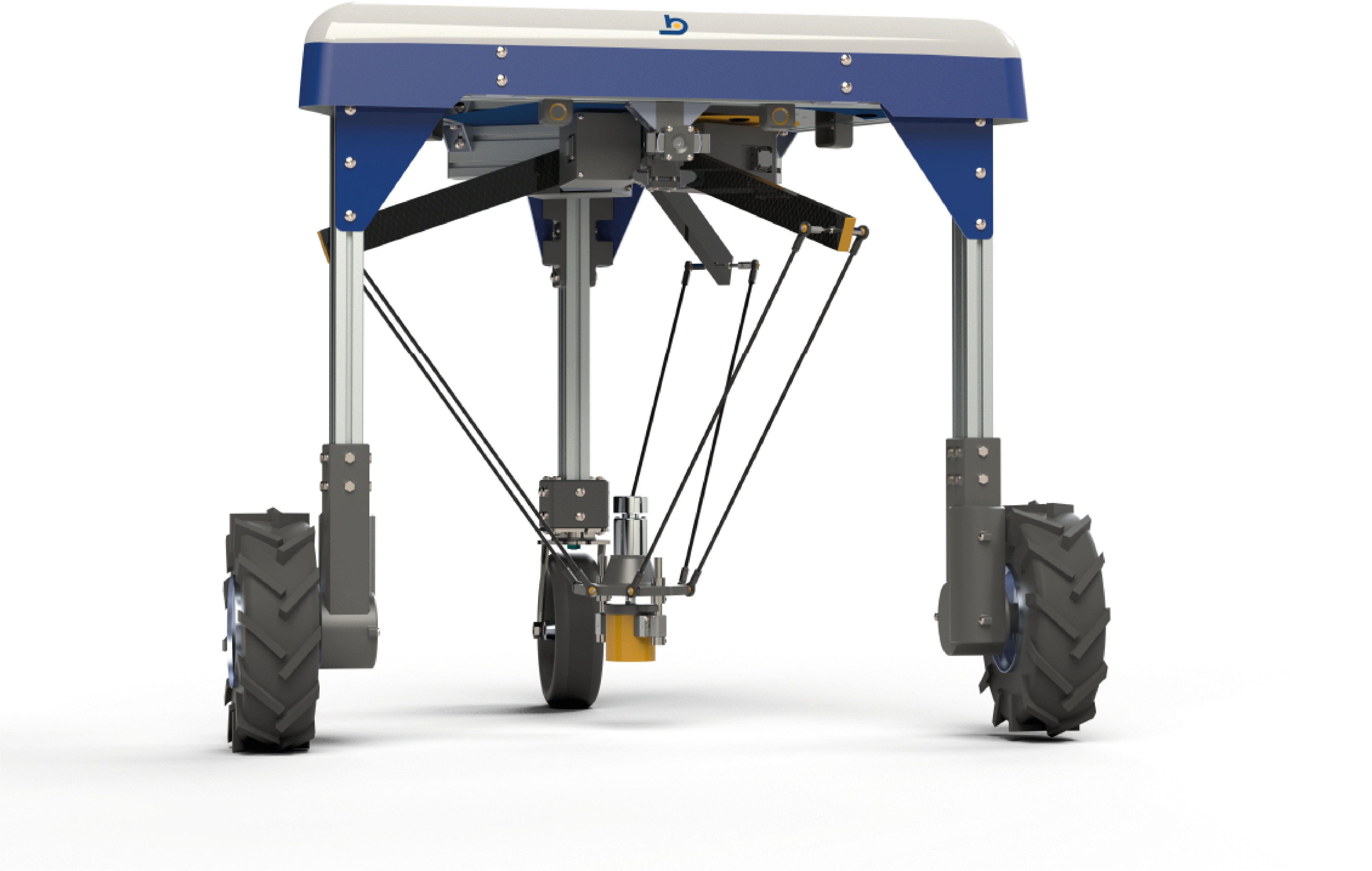
These posed problems are the ones being solved by the Weed-whacker, by being autonomous, the amount of human labour is minimized. By using cameras to recognize every instance of weed and being precise on removing them, herbicides are no longer necessary. The robot will run on electricity, preferably from a renewable source, so the process will not amount to any further global warming. By keeping the robot light, the energy consumption can be held low, and the impact on the soil minimal. Eventually, this solution can be optimized to remove all the weeds in all kinds of fields, and being a mechanical instead of a chemical solution, the weeds have no chance of growing any resistance against our robot.
This project is commissioned by Odd.Bot.
Team 4 In-depth Dredging
Autonomous Dredging Robot
In 2012 Natuurmonumenten started a project to restore the Markermeer and create the Marker Wadden, which is an artificial island group located in the Markermeer. This island group is created with the help of the silt from the bottom of the Markermeer. This is where Boskalis, one of the largest dredging companies of the world, steps in. Natuurmonumenten asked Boskalis to come up with a solution to automate the relocation of the silt. Since Boskalis uses large dredging ships to remove silt from the bottom of waterways and the mobilisation of such ships is rather costly and time consuming, Indepth Dredging has been assigned the task to design and develop a robotic solution.
We are going to create an autonomous robotic system that will be able to remove and relocate the silt from the bottom of the Markermeer to a dumping location, from where the silt is pumped to an artificial island. Note that the system will only be concerned with relocation of silt, not the creation of an artificial island.
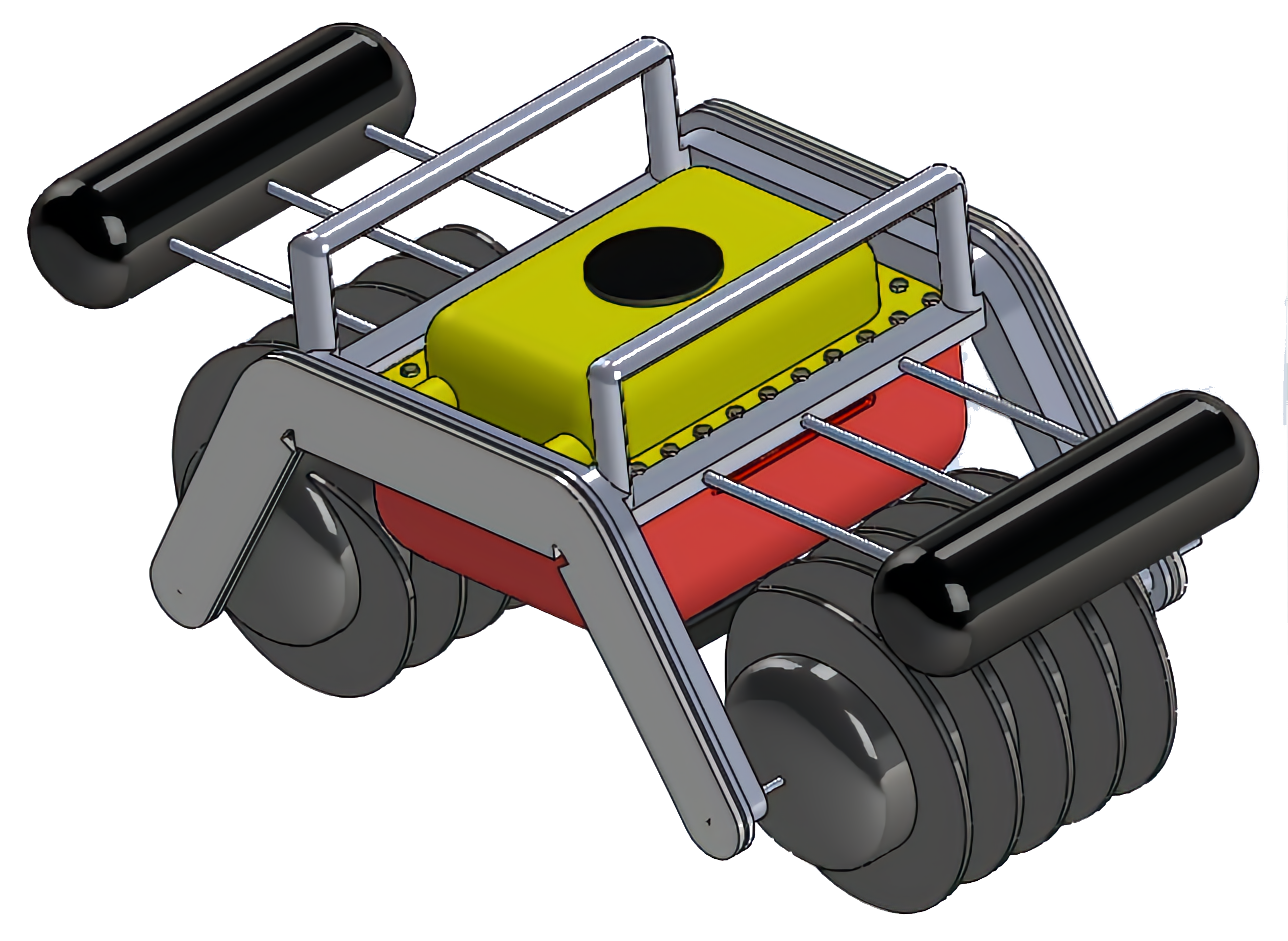
This project is commissioned by Boskalis & Natuurmonumenten.
Team 5 Blooming Robotics
Algae Removing Vessel
This summer, the Dutch waters were widely inhabited by an unwanted visitor: Blue-green algae (Blauwalg). These micro-organisms clump together in the morning to form a gross green gooey mess. The algae, or cyanobacteria to be more accurate, is highly toxic and hinder the practice of water related activities. Not only within the Netherlands do we suffer from these tiny creatures. Blue-green algae is a world wide problem.
Employed by the company Deltares, we from Blooming Robotics are tasked to solve this dilemma. We are working to create an autonomous vessel that will traverse contaminated water bodies and scoop up the layer of algae that drifts on top.
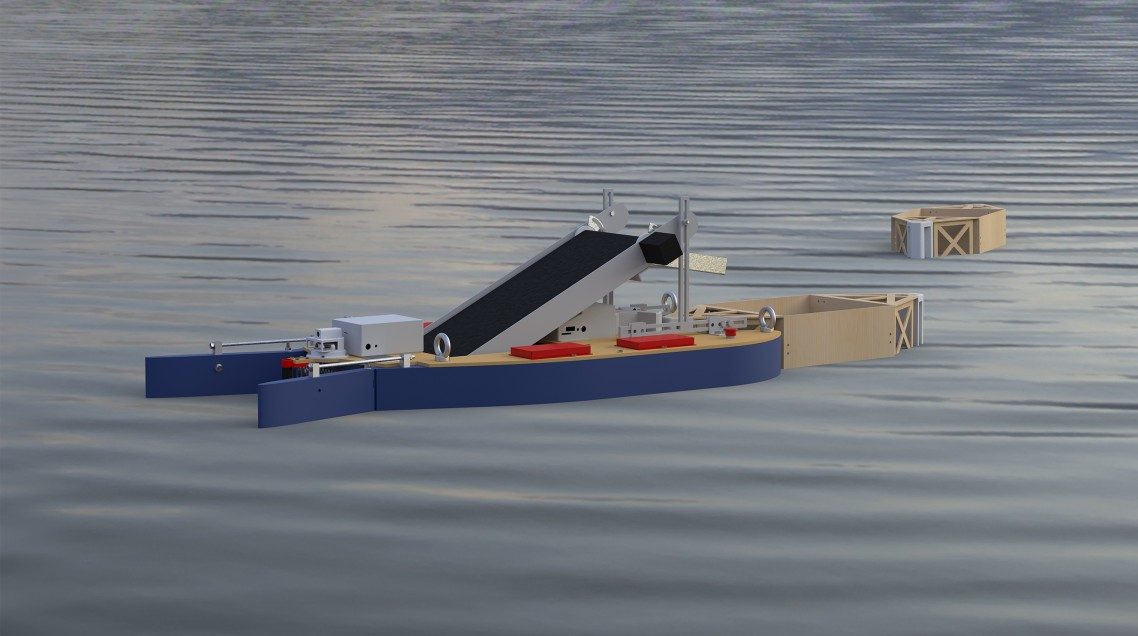
This project is commissioned by Deltares.
Team 6 DORST.
Automated Coffee Corner
Dorst. Robotics has been tasked by the Science Centre, the technology museum of the TU Delft, to automate their coffee corner. The goal of this project is to make ordering a drink an experience in line with the other exhibits in the museum, meaning it should be fun and educational.
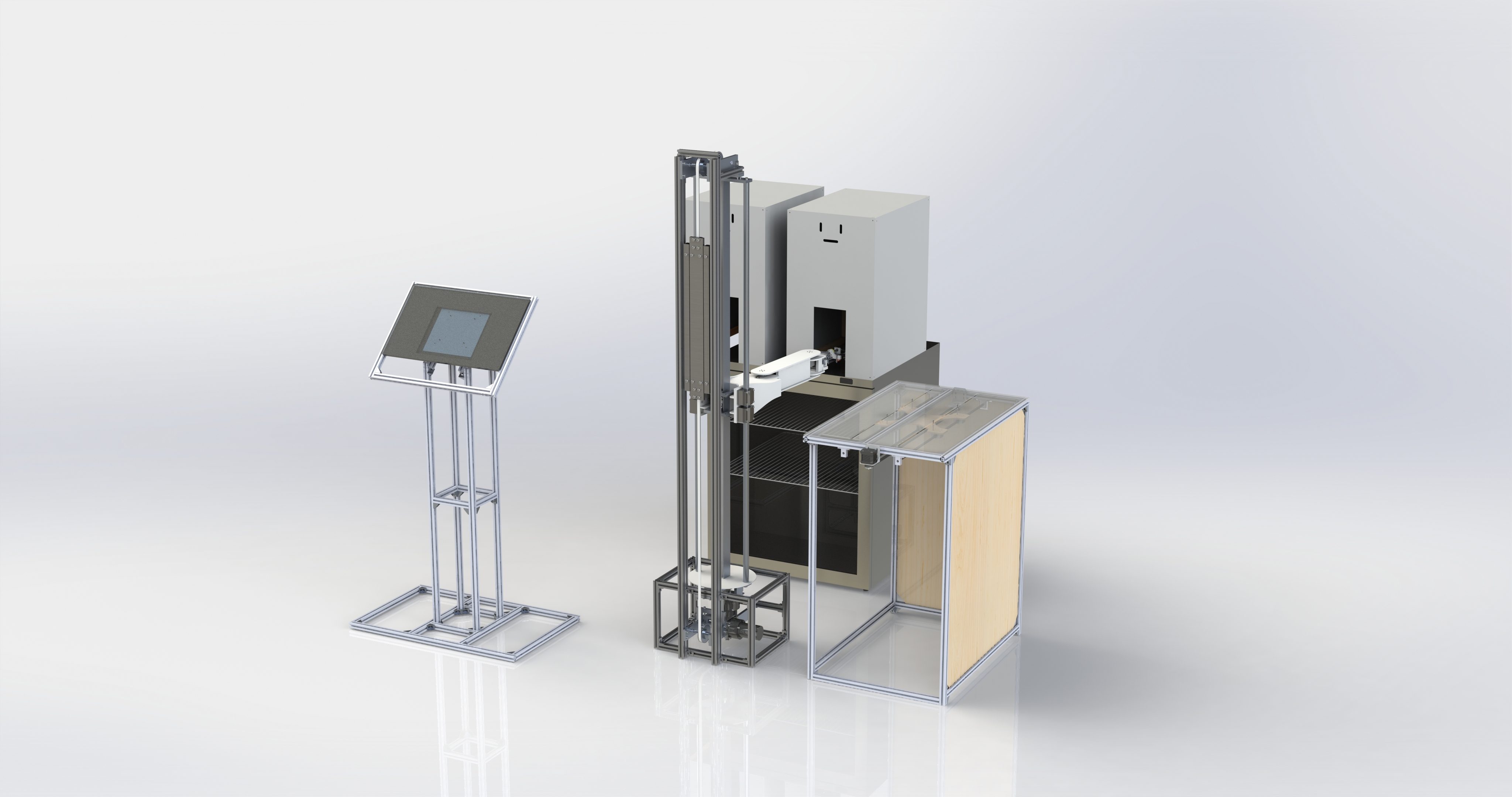
This project is commissioned by the Science Centre.
Team 7 bHive
bHive
Team bHive has been asked by the TU Delft’s MAVLab to create a portable drone show that helps put drones and autonomous aerial vehicles in a more positive light. The MAVlab (or Micro Air Vehicle lab) researches new ways to use and build different types of unmanned flying vehicles. They have created many new use-cases for autonomous drones, but they have noticed that the new developments are not always widely met with great excitement. People tend to be scared of drones and autonomous robots.
The team takes inspiration from a swarm of bees to create a self contained “bHive” from which drones can be deployed autonomously to begin the show. Part of the assignment was to make use Ultra Wide Beacons provided by the MAVLab to further the technology. These beacons will assist the drones in communication, as well as localization. The team is developing their own drones, combining off the shelf parts with self-made components to create a lightweight, agile and low cost aerial vehicle. The “hive” or deployment enclosure will also be developed by the team.
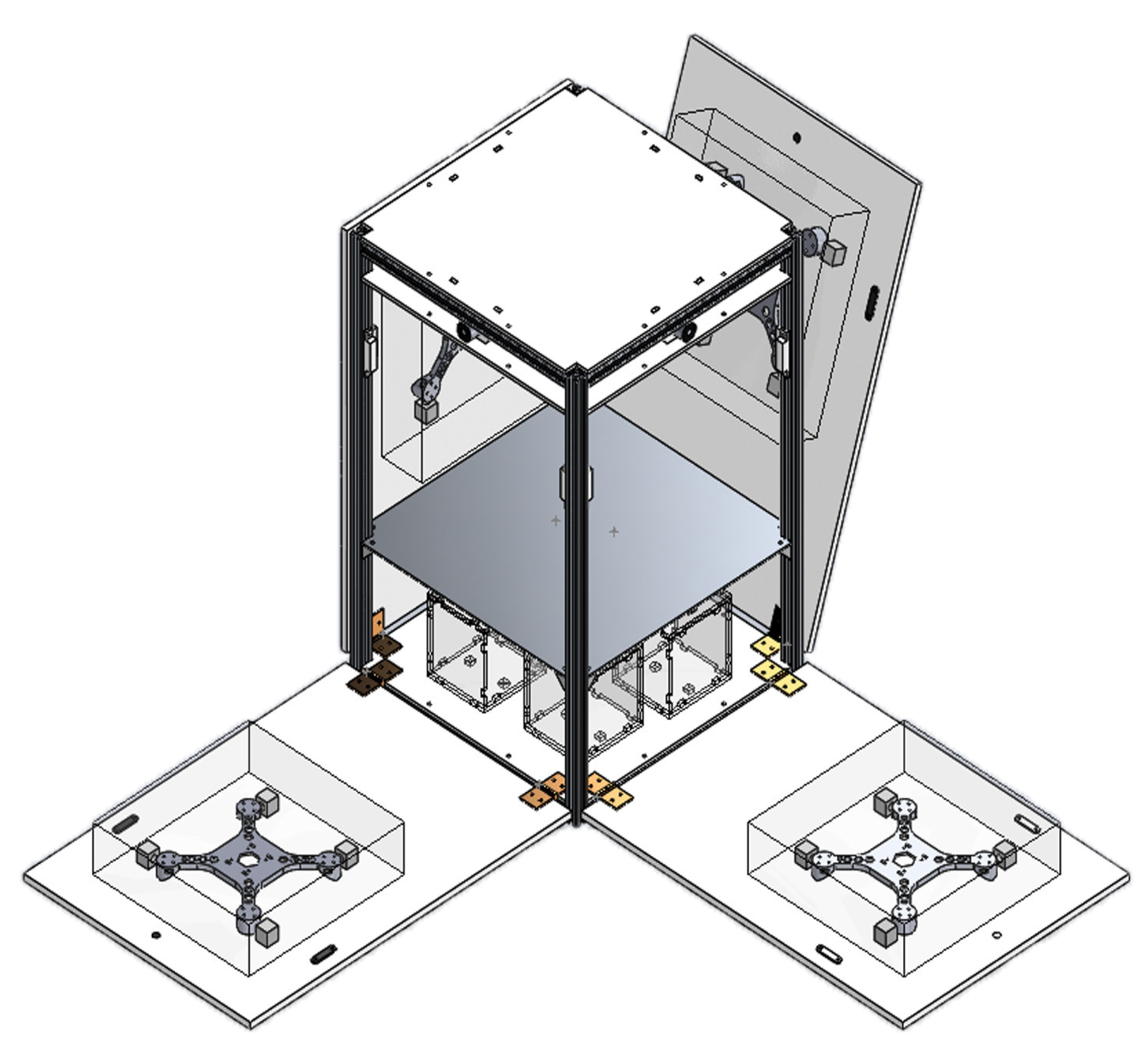
This project is commissioned by MAVLab.
Team 8 nFocus
Engine Inspection Robot
KLM Engine Services (ES) is one of the largest aircraft engine maintainers in Europe. However, the process of maintaining aircraft engines can certainly be improved. Currently, fully servicing an engine will take about 80 days. The initial inspection of an incoming engine can take upwards of two shifts, taking the time and energy of two mechanics. Exploring new technological solution to existing problem will help KLM ES remain a forerunner within the industry. Successfully analyzing the current maintenance process and successfully integration of new technologies into the process can teach very valuable lessons about what the future for aircraft engine maintenance could look like.
See other projects that were made in RoboHouse
Back to overviewKLM ES has tasked the team of nFocus to develop a robot that can autonomously perform the initial inspection of a new type of aircraft engine. Their fresh view from the outside will give KLM ES a new perspective about the topic of robotics. The students, each with a different background are experienced in solving problems on their part of the complex problem. Not only taking the technical aspects into account, but also how a robot should be integrated in the current and future process of the engine servicing.
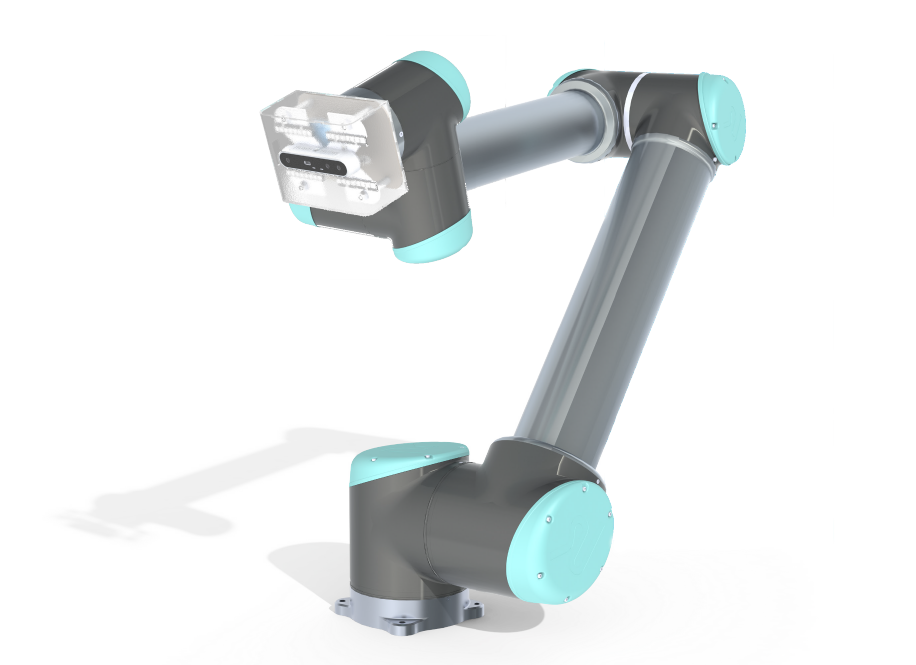
This project is commissioned by KLM Engine Services.